In addition to delivering excellent results, the code is easy to use and highly versatile.
Simulation Code for the Design of Small Compressors
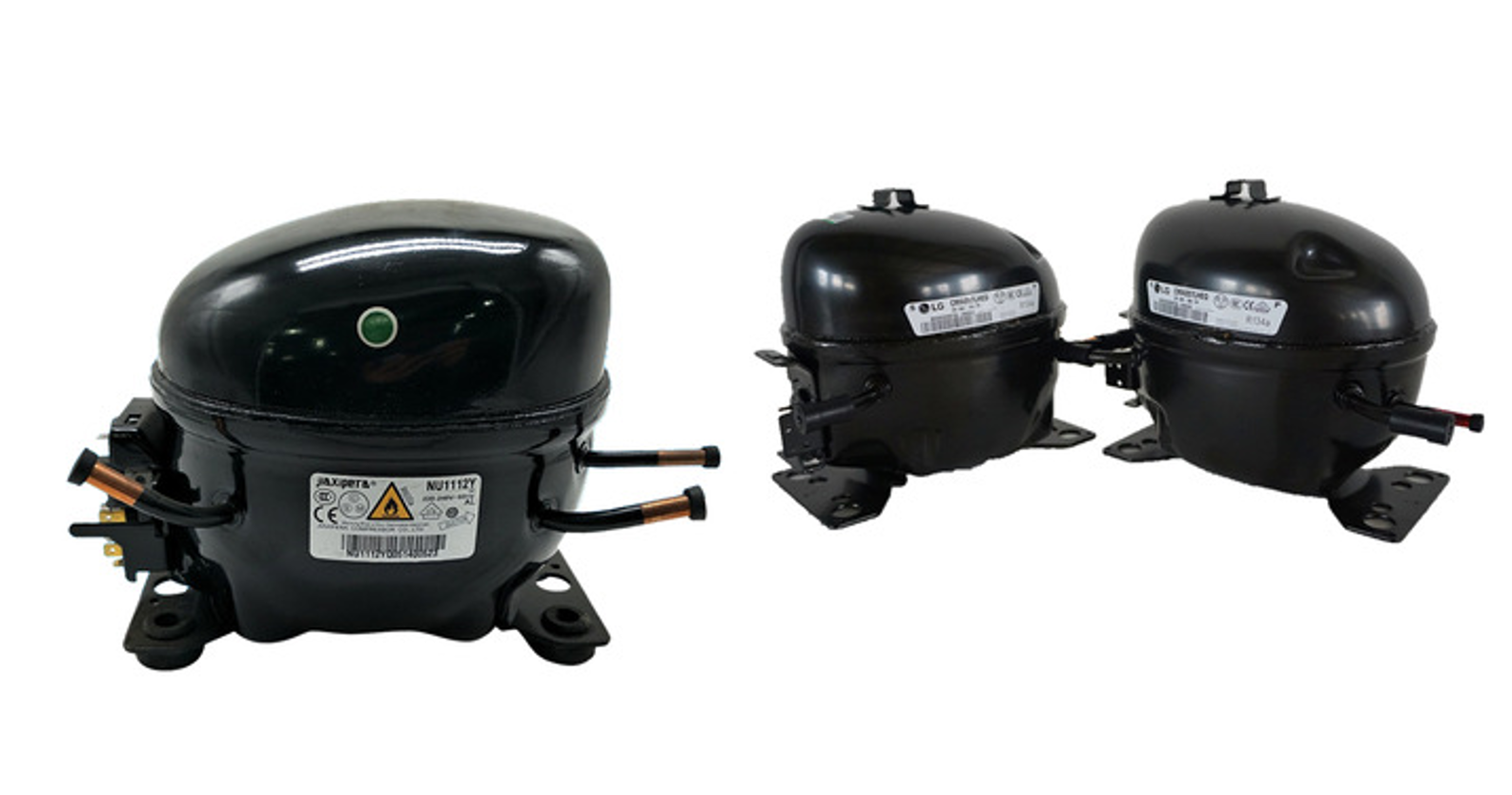
Our activity led to the development of a numerical simulation tool for positive-displacement compressors for small refrigerators. The tool consists of three specially developed software programs:
- A. a graphical interface to generate the input file for the compressor simulator,
- B. the compressor’s numerical simulation code,
- C. a graphical interface for viewing and processing the results obtained by the simulator.
The graphical interfaces for generating input and output files are designed specifically for the individual machine.
The first interface enables:
- construction and modification of the compressor diagram
- definition of the fundamental dimensions of the various components
- finally generation of the input-data file containing highly specific details about the individual components and the fluids used
Before generating the file, the software checks the formal accuracy of the values entered for the various compressor components and on the diagram, to minimize the possibility of error and ensure the simulation is successful.
The second interface is for viewing the simulation results of each element, and hence for combining different dimensions and objects. In addition to detecting the cyclic variation characteristics of the main quantities, the interface automatically provides information about the machine’s overall performance (power, efficiency, COP, cooling capacity, etc.), and can perform an FFT analysis of the main quantities of the compressor’s various components.
The actual simulation software has its own graphical interface that allows you to load an input file, and check the status of the simulation. It displays the iteration, power, torque and flow of refrigerant through the cylinder, as well as calculation errors for each of the elements that make up the compressor.
The simulation code uses a one-dimensional model for pipes, and a zero-dimensional model for volumes. It also allows you to solve heat exchange equations for conduction and convection. Pressure, temperature, mass flow, and other specific quantities relevant to the components are calculated, and this allows you to define the system’s performance. The code can work with air, R600A, R404A, R290, and R134A.
The simulation results are saved to .csv files, so can be opened and processed by the most popular spreadsheet programs.